News
2023/4/19
PACKNERS GmbH installs the world's 600th rotary die cutter from BOBST for the production of high-quality corrugated board packaging
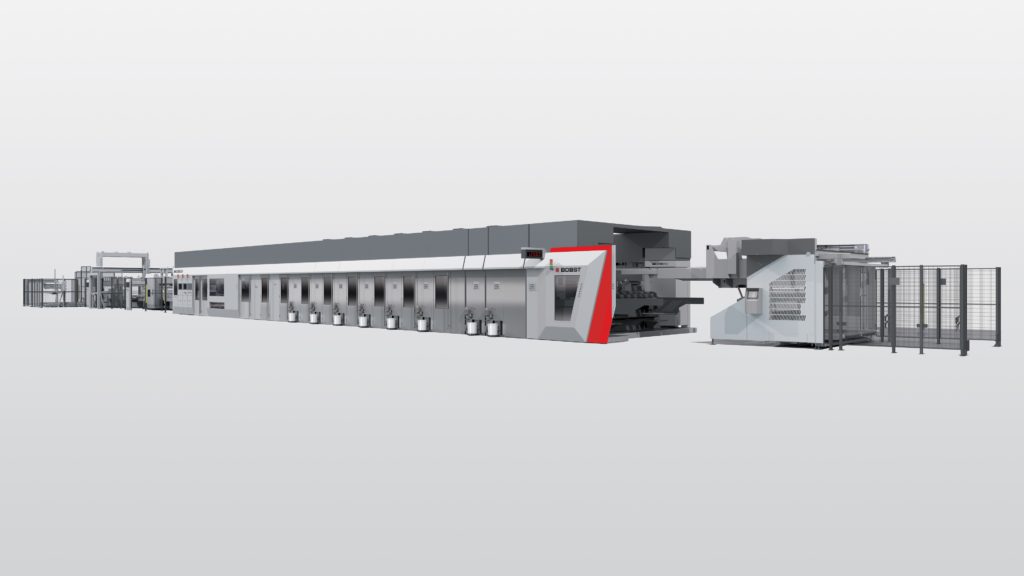
At the end of 2023, BOBST will deliver its 600th rotary die cutter worldwide, underlining its leading position also in this segment of the packaging market. The anniversary machine - a MASTERLINE DRO with six printing units - will be installed at the new PACKNERS GmbH plant in Emsbüren in north-west Germany. "We want to use this high-end rotary die cutter to create additional opportunities for new market segments in the production of high-quality corrugated board packaging" explains Stefan Gausepohl, Head of Sales & Marketing and, as an authorized signatory a member of the PACKNERS management team.
The MASTERLINE DRO is the flagship rotary die cutter from BOBST. It can be configured for inside and outside printing in a single pass. It is also characterized by a uniquely high degree of automation. PACKNERS uses all the automation options offered by BOBST. In addition to the automatic anilox roll change, fully automatic register settings with the Start & Go system and the integrated anilox roll cleaning, the rotary die cutter will be equipped with a MULTILOADER pre-feeder, a SPEEDSTACK stripping unit and bundle stacker, along with a SPEEDPAL palletizer. As a result, PACKNERS will have the ability to fully exploit the high productivity of up to 12,000 sheets per hour while achieving the fastest job changes.
Several features of the MASTERLINE DRO support the shortest possible set-up times: For example, the operators can change plates in the idle printing units while the rest of the line is producing other jobs. The Start & Go system reduces the time needed for print settings by up to 80%. A fully automatic trolley allows four anilox rolls to be changed from one flexographic printer to another in less than ten minutes during production. The integrated anilox roll cleaning system in turn, enables automatic washing of anilox rolls without any operator intervention - while the processing line is still producing. In addition, there are fully motorized settings.
The high level of automation of the rotary die cutter will not only improve the profitability but also the sustainability at the new PACKNERS plant. It guarantees the highest stability and safety in production, which is reflected in the form of consistent quality and minimized waste. For example, the Start & Go system reduces start-up waste by up to 38%, while the new inking system reduces ink loss during wash-ups by around 50%.
In addition to the rotary die cutter, PACKNERS has ordered an FFG 8.20 EXPERTLINE inline machine with two printing units from BOBST for its new plant, as well as a MASTERFOLD 230 A4 folding box gluer with a working width of 2.3 m and a SPEEDPACK automatic packing system including strapping. Besides, the company will have its FFG 8.20 EXPERTLINE with four printing units, which was commissioned at its previous site beginning of 2021 moved to the new plant. Plant manager and authorized signatory Christian Wala: "With this inline processing line, we also use all the automation functions offered by BOBST. That's why we can fully utilize its production output: up to 24,000 boxes per hour of transport and shipping packages on many jobs." PACKNERS also achieves top values with it in terms of set-up times: on average, they are in the single-digit range. The good experience with the FFG 8.20 EXPERTLINE formed the basis for intensifying the partnership with BOBST.
"The technology we purchased for our new plant is the best and fastest currently available on the market. We are convinced of that," Gausepohl says. "The fact that our MASTERLINE DRO happens to be the 600th rotary die cutter installed by BOBST worldwide, underscores the wisdom of our investment decision. We are just one of many owners in the global market." Depending on how customer requirements develop, PACKNERS can have printing units for high-quality inside printing added at a later date.
Bobst Lyon has been offering machines for printing and rotary die-cutting of corrugated board since the 1920s and has continuously developed them in close cooperation with customers all over the world. BOBST customers on all five continents work with machines from this product line. About half of the machines are installed outside Europe.
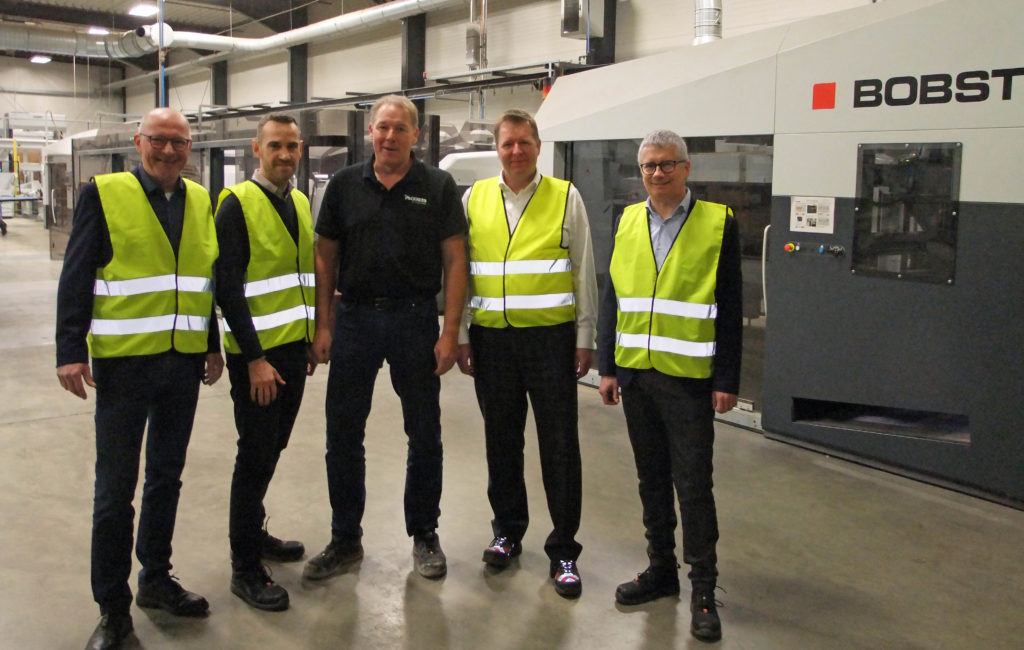
Olivier Portal, Bobst Lyon Technology Sales Manager for Germany and Switzerland: "The MASTERLINE DRO combines more than 30 years of BOBST experience in building rotary die cutters. Some of the first DRO rotary die cutters are still in use today. With its unique performance combined with the highest production quality and the simplest intuitive operation, PACKNERS will be able to tap into new growth potential for high-quality corrugated packaging. We are very pleased that the company has chosen our upmarket flexo printing and rotary die-cutting production line."
BOBST is committed to shaping the future of the packaging industry. The means to this end is its industrial vision, which is built on the key pillars of digitization, automation, networking and sustainability. "The new PACKNERS plant in Emsbüren will become a prime example of how this vision becomes reality," Portal said.
- Category
- Featured Stories
- Packaging