アーカイブ情報
2024/6/5
【半導体】日本電気硝子、ガラスセラミックスコア基板「GCコア」開発。高速でクラックレスかつ経済的な微細ビア加工を実現
日本電気硝子は、次世代半導体パッケージに利用が期待されるガラスセラミックスコア基板「GCコア(TM)」を開発した。
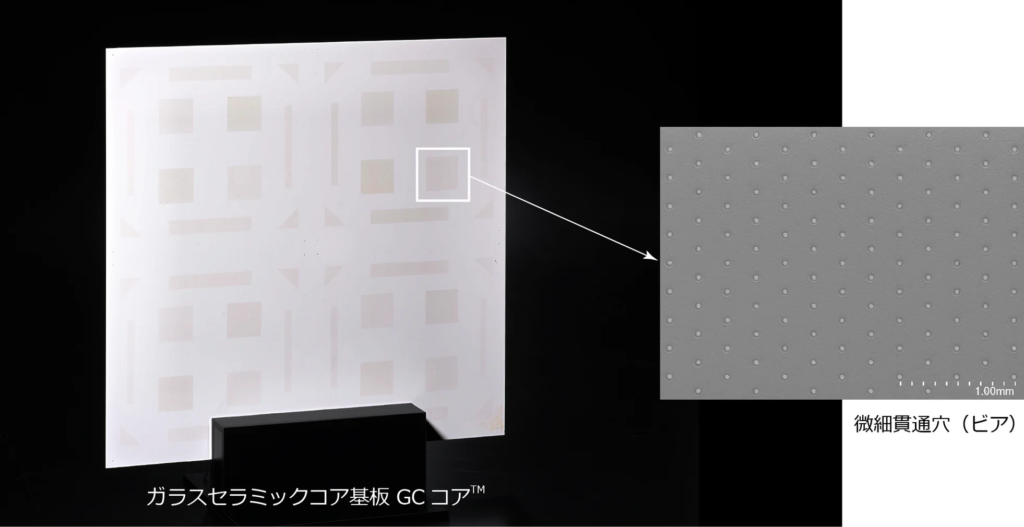
近年、データセンターの需要の増大や生成AIなどの普及によるデータ通信量の増大に伴い、これらを支えるインフラ等に使われる半導体にはさらなる高性能化や低消費電力化が求められている。
半導体の性能向上には回路の微細化やチップレット(※1)化、基板の大型化による対応が不可欠となる。しかし、従来の樹脂製のコア基板(※2)では微細化が困難であるとともに、複数の半導体チップを搭載した場合や基板を大きくした場合に基板が変形するという剛性上の課題があった。
このため、樹脂製のコア基板に替わる次世代の材料として、電気的特性、剛性、平坦性などに優れたガラスを用いたコア基板の開発が進められている。今回、同社が開発した「GCコア(TM)」は、ガラス粉末とセラミックス粉末の複合材を用いたコア基板で、ガラスを用いたコア基板の特性に加え、微細貫通穴(ビア)の加工が容易という特長を持つ新素材。
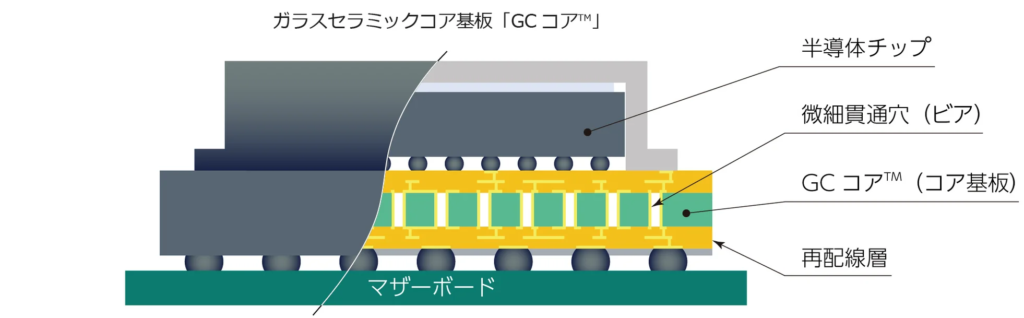
GCコア(TM)の特長は次の通り。
1.CO2レーザーにより穴あけ加工が可能
コア基板には、表裏に形成された微細な金属配線を電気的に接続するため、微細貫通穴(ビア)を形成する必要がある。
割れない&高速加工
一般的なガラス基板の場合、CO2レーザーにより穴を開けると、一定の割合でクラック(割れ目)が入り、基板の破損につながる恐れがある。GCコア(TM)は、セラミックスの特性(※3)も有しているため、高速でクラックレスの穴開け加工が可能。
経済的&量産コスト低減の期待
一般的なガラス基板の場合、クラックを避けるためレーザー改質とエッチングを用いて穴加工する方法が一般的だが、この方法は技術的難易度が高く加工に時間が掛かるほか、設備投資が必要になる。GCコア(TM)は、一般に広く普及しているCO2レーザー加工機で穴加工ができるため経済的で、量産コストの低減が期待できる。
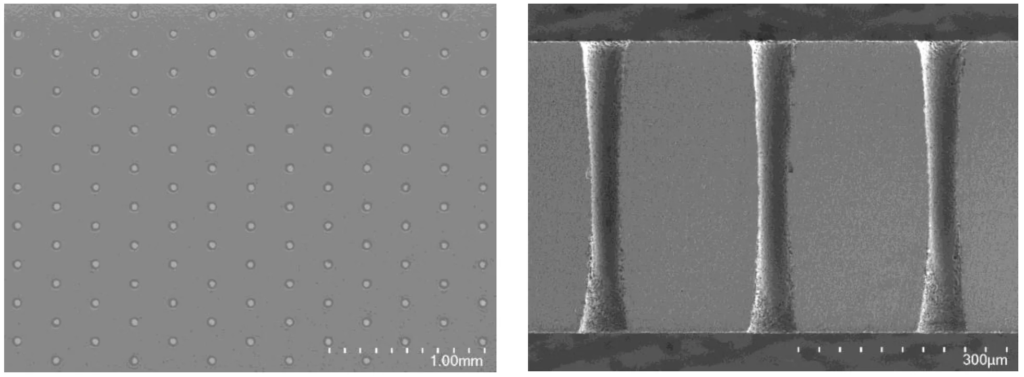
2.低い誘電率と誘電正接
ガラスセラミックス材には、同社が独自に開発したLTCC材料(低温焼成セラミックス)を使用しており、誘電率・誘電正接(※4)が低く、信号の遅延や誘電損失の低減を実現している。
3.基板の薄型化が可能
GCコア(TM)は、ガラス基板と比べて強度が高いため、基板を薄くすることができ、半導体の薄型化に貢献する。また、割れにくいため半導体パッケージの生産プロセスにおけるハンドリング性が向上する。
4.ニーズ合わせた仕様変更が容易
GCコア(TM)は、ガラスとセラミックスの組成や配合比を変えることにより、ニーズに合わせた特性を実現できる。誘電特性に優れた低誘電率タイプ以外にも、樹脂基板の熱膨張に合わせた高膨張タイプ、強度に優れた高強度タイプなど幅広い用途に対応できる基板の開発を可能にする。
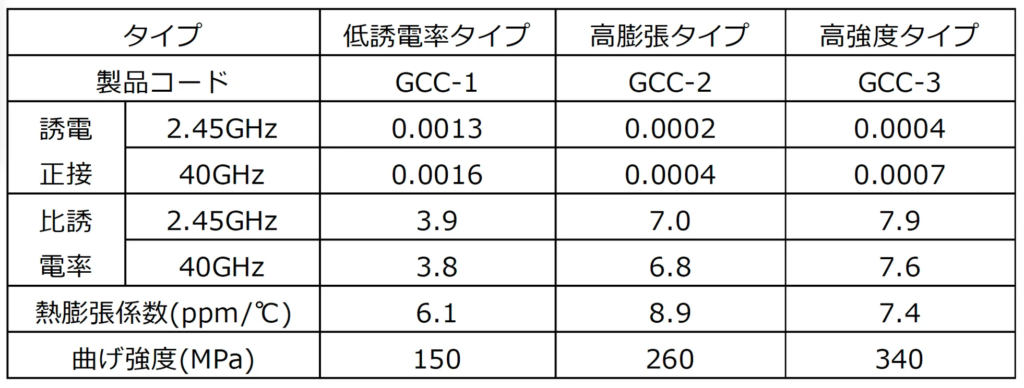
現在、300mm角の基板の開発に成功している。2024年内には515×510mmへの基板の大型化を目指し開発を進めている。300mm角の基板については2024年6月12日から東京ビッグサイトで開催される「JPCA Show 2024」(小間番号No.6H-01)に出展する。
※1 チップレット
機能の異なる複数の半導体チップを1つの基板上に高密度に実装し、処理速度を向上させる半導体パッケージの先端技術。
※2 コア基板
半導体チップを載せる土台となる基板材料。
※3 セラミックスの特性
セラミックスは結晶構造を持ち、結晶内の原子やイオンが強力に結びついている。そのため、セラミックスは外部の力によって変形しにくく、クラックが入りにくい特性がある。
※4 誘電正接
誘電体が分極するときのエネルギーの指標。誘電正接が小さいほど、電磁波のエネルギーが熱に変換されにくくなり信号の減衰が抑制される。
- カテゴリー
- コンバーティングニュース